Continuous Carburizing, Carbonitriding, or Neutral Hardening
Founded in 1989 | IATF 16949 / ISO 9001 Certified QMS | Automotive CQI-9 | On-Site Laboratories
Read About Our Cost-Effective Low-Distortion Carburizing for Transmission Gears! Ask The ExpertsFounded in 1989TS 16949 / ISO 9001-2009 CertifiedOn-Site Laboratories
Continuous Carburizing Treatments for Steel Parts
You'll be pleased to know that we have the equipment to batch carburize up to 550,000 pounds of parts every day! When you choose American Steel Treating for a batch carburizing service, you'll never have to worry about getting your entire order on time and up to quality standards!
About Our Continuous Carburizing Treating Process
Carburizing is a high temperature heat treat process 898°to- 954° C (1650° to 1750°F) where
a higher percentage of carbon, i.e. 0.80 – 1.20% is added to the atmosphere on material’s
typically containing < 0.27% carbon. The depth of carbon penetration is dependent upon
time and temperature of the treatment and can also be influenced by the furnace type.
After carburizing, the part is hardened by lowering to a specified hardening temperature, stabilizing and then quenching in a suitable media, immediately followed by tempering.
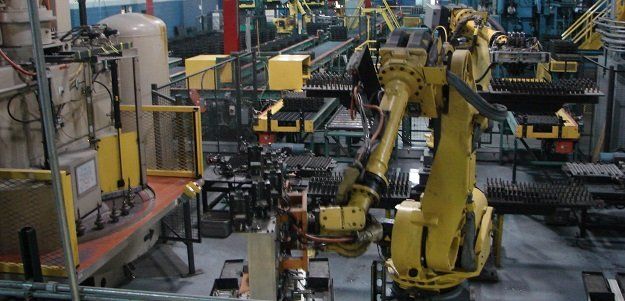
Continuous Carbonitriding
Carbonitriding is similar to carburizing, whereas it is performed at process temperatures ranging from 816° to 949° C (1500° to 1740°F). The process is usually done on materials that have lower hardenability such as screw machine parts made from SAE 1215 material or stampings made from a low carbon steel.
Carbonitriding uses a hydrocarbon gas with ammonia (nitrogen) added to increase the hardenability. The nitrogen assists in forming martensite in the low carbon steels but is an austenite stabilizer and could result in considerable retained austenite after quenching. After carbonitriding, the parts are usually quenched in a liquid media, tempered, cryogenically treated (optional) and based upon part geometry, may be heat set to reduce distortion and return the part to its desired dimensions. NOTE: Carbonitriding should not be confused with nitriding.
Continuous Neutral Hardening
Neutral hardening is defined as the percentage of the carbon in the atmosphere being equal to the percentage of the carbon in the steel. For example, SAE 4140 has 0.40% of carbon so the steel mill must provide a range of carbon from 0.38% to 0.43% in order to meet the specification.
In turn, the heat treater must maintain a carbon potential that is neutral or equal to 0.40%. This term usually is defined as heating to a suitable temperature, typically 829° to 857° C (1525° to 1575°F) followed by rapid cooling or quenching in a media, such as oil. After quenching, the microstructure is untempered martensite which is very unstable, so tempering is performed to temper the martensite and stabilize / toughen the base material.
We are compliant with Caterpillar standards for carburization.